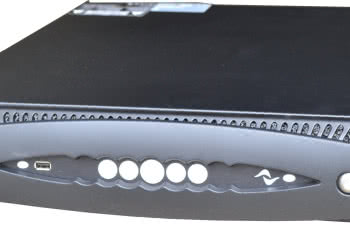
X4L - wzmacniacz z DSP z serii X
Biznes „nagłośnieniowy” – w porównaniu z innymi dziedzinami techniki (np. przemysłem samochodowym, czy ...
Kontynuując rozważania na temat głośników estradowych rozpoczęte w poprzednim numerze, w drugiej części artykułu skupię się na konkretnych przykładach ich uszkodzeń i postaram dowieść, że stosunkowo często winę za taki stan rzeczy ponoszą producenci, a nie nabywcy.
W związku z powyższym nie będę opisywał błędów popełnianych przez użytkowników aparatury estradowej, których konsekwencją również bywa destrukcja przetworników, bo jest to temat na oddzielny artykuł. Skupię się wyłącznie na wadach fabrycznych, wynikających z „oszczędnościowych” technologii produkcyjnych i braku właściwej kontroli jakości, co jest niestety dość powszechnym zjawiskiem przy masowej skali produkcji i umiejscowieniu jej w krajach oferujących tanią siłę roboczą.
Przy podejściu nastawionym głównie na „przerób” i minimalizację kosztów liczą się nawet najmniejsze oszczędności, a przecież oczywistym jest, że każdy detal głośnika ma znaczenie z punktu widzenia jego jakości, i że decyduje o niej jego najsłabszy element. Gorzej, jeśli dany wyrób składa się głównie z „najsłabszych elementów”, bo wtedy prawdopodobieństwo usterki rośnie w trudny do przewidzenia sposób. Takie przetworniki często nazywane są produktami „budżetowymi”, choć należy jednak zauważyć, że w tej grupie można spotkać zarówno całkiem przyzwoite wyroby, jak i takie, na które należałoby spuścić litościwą zasłonę milczenia, gdyby nie to, że jednak trzeba za nie płacić jakieś pieniądze, i że często są to pieniądze zmarnowane. Również dlatego, że marnych głośników nie opłaca się naprawiać, podobnie jak niektórych wyrobów elektronicznych, bo w wielu wypadkach koszt profesjonalnie przeprowadzonego remontu byłby większy niż cena nowego głośnika.
Jednak nawet drogie głośniki wyższej klasy również miewają swoje bolączki, choć na szczęście często daje się je wyeliminować, o ile oczywiście specjalista wie, gdzie tkwi ich słaby punkt.
W głośnikach z wyższej półki cenowej często bywa tak, że zawodzi tylko jeden element i z punktu widzenia użytkownika najbardziej zawodne są cewki, bo uszkodzenie uzwojenia czy karkasu definitywnie eliminuje przetwornik z użycia, i są to najbardziej „spektakularne” awarie i zapewne najczęściej spotykane.
Jednak z punktu widzenia profesjonalnego serwisanta najbardziej istotny jest poprawnie zaprojektowany i wykonany obwód magnetyczny, bo jest to jedyny oprócz kosza element konstrukcyjny głośnika, na jakość którego serwis nie ma wpływu. Niestety jest to również element najdroższy, którego wykonanie kosztuje wielokrotnie więcej, niż pozostałych elementów głośnika.
Szukając oszczędności firmy starają się więc „odchudzać” obwody, i to nie tylko stosując magnesy neodymowe. Da się zaoszczędzić również na ferrytach, których kiepska jakość powoduje, że pękają bez żadnych udarów mechanicznych, albo na stali, używając jej najtańszych gatunków, czy nawet na grubości wykonywanych z niej nabiegunników, czemu chciałbym poświęcić teraz kilka słów.
Warto zauważyć, że grubość tego elementu w pozornie podobnych obwodach, stosowanych np. w przetwornikach niskotonowych dużej mocy, potrafi różnić się znacząco – w skrajnych przypadkach nawet dwukrotnie. Jest to o tyle istotne, że grubość górnego nabiegunnika (czyli tego, który mocowany jest do kosza) ma decydujący wpływ na możliwość zastosowania cewki o odpowiedniej do danej aplikacji wysokości uzwojenia. Jeśli np. chcemy uzyskać dobrze brzmiący bas i jednocześnie maksymalną moc, przy dużej amplitudzie dopuszczalnych wychyleń membrany, to uzwojenie cewki musi mieć odpowiednią wysokość. To z kolei „wymusza” zastosowanie jak najgrubszego nabiegunnika, aby uzwojenia nie wychodziły w trakcie pracy poza pole magnetyczne w szczelinie, i aby była możliwość uzyskania jak największej wartości parametru X-max.
Z punktu widzenia „ekonomii produkcji” jasne jest, że nabiegunnik o grubości 12 mm lub większej (najgrubszy, jaki spotkałem w mojej praktyce, miał bodaj 15 mm) będzie droższy niż taki o grubości 8 mm, więc wiele firm produkuje głośniki tak, jak jest im wygodnie i taniej, w konsekwencji czego wysokie cewki współpracujące ze zbyt cienkimi nabiegunnikami przejawiają tendencję do przegrzewania się w obszarze skrajnych uzwojeń. Taki przypadek pokazuję na zbiorczej fotografii 3 cewek, gdzie w każdej z nich skrajne uzwojenia uległy albo przegrzaniu (cewka po lewej stronie), albo całkowitej destrukcji.
Z kolei nabiegunnik dolny, w niektórych głośnikach o wiele bardziej masywny niż górny, wykonywany może być w procesie zwykłego toczenia blachy stalowej, ale również w formie odkuwek ze specjalnych stali niskowęglowych, jako jeden element, który potem tylko dotaczany jest na dokładny wymiar. Duże znaczenie ma również użycie odpowiedniej stali o niskiej zawartość węgla, która ma lepsze własności magnetyczne od zwykłej stali stopowej, ale jest o wiele droższa.
Tyle że te kosztowne i pracochłonne technologie obecnie są stosunkowo rzadko wykorzystywane, a jeśli już, to jedynie w najdroższych głośnikach, których cena czasem może okazać się nie do zaakceptowania dla przeciętnego użytkownika. Jednak na rynku znajduje się jeszcze wiele starszych głośników wykonywanych wg. starej, dobrej szkoły, i są to produkty, które z pewnością warto szanować i w razie potrzeby regenerować, bo górują pod wieloma względami nad różnymi współczesnymi „wynalazkami”.
Niezwykle istotne jest, aby obwody magnetyczne były poprawnie zmontowane i sklejone, przy czym pisząc o poprawności montażu mam na myśli m.in. zachowanie takich samych wymiarów szczeliny na całym jej obwodzie, bo niestety stosunkowo często spotykam w swojej praktyce przypadki, gdy już na oko można stwierdzić, że szczelina nie jest równa.
W takim wypadku trudniej jest wycentrować cewkę, a nawet jeśli uda się tak zmontować głośnik, żeby cewka nie obcierała, to pole w szczelinie nie jest jednorodne, a „przy okazji” cewka gorzej się chłodzi w miejscach, gdzie szczelina jest węższa.
Skoro było już o obwodach, to teraz kilka zdań o koszach głośnikowych, do których są one mocowane. W głośnikach profesjonalnych stosowane są wyłącznie kosze odlewane ze stopów metali lekkich, głównie z aluminium. W sprzęcie budżetowym często wykorzystywane są kosze wykonywane jako wypraski stalowe i w przypadku ich kiepskiej jakości mogą również sprawiać pewne problemy. Np. zbyt cienka blacha powoduje, że kosz nie ma odpowiedniej sztywności i może odkształcić się w trakcie mocowania do obudowy, co skutkuje często przekoszeniem membrany wraz z cewką i w konsekwencji jej obcieraniem o nabiegunniki. Błędem w sztuce jest montaż dużych i ciężkich obwodów na takich koszach, bo nie są one często w stanie przenieść tak dużych obciążeń, szczególnie „dynamicznych”, np. w trakcie transportu.
Kolejnym problemem bywa sposób mocowania obwodu do takiego kosza, bo niektóre firmy ze względów oszczędnościowych stosują zamiast wkrętów nity, co jest bardzo złym rozwiązaniem. Zaś zupełnym nieporozumieniem jest mocowanie obwodu do kosza jedynie za pomocą kleju, a takie głośniki też znajdują się niestety na rynku i należy je omijać jak najszerszym łukiem. Tyle że przed odpadnięciem obwodu od kosza trudno się zorientować, że trzyma go jedynie warstwa kleju. Jednak nawet kosz odlewany w formach ciśnieniowych też może być wadliwy, bo widziałem już takie, które położone na równej płaszczyźnie bujały się, jak łódka na falach, co oczywiście jest dyskwalifikacją, bo trudno w takim koszu uzyskać osiowość cewki w stosunku do szczeliny, gdy płaszczyzny klejenia zawieszeń i mocowania magnesu nie są równoległe. Miałem również do czynienia z koszami produkcji dalekowschodniej, które po pewnym czasie magazynowania „znikały” w oczach, czyli utleniały się, no ale to już skrajny przypadek wady fabrycznej.
Podsumowując: kosz stanowi bardzo istotną „bazę” dla mocowania obwodu magnetycznego i membrany z zawieszeniami, dlatego niezwykle istotna jest dokładność jego wykonania i odpowiednio zaprojektowany kształt oraz materiał, z którego jest wykonany. Jednak nawet kosze odlewane metodą wtryskową w formach ciśnieniowych potrafią cierpieć na różne wady fabryczne, jak choćby zbyt cienkie ścianki, co może spowodować pękniecie kosza przy upadku zestawu głośnikowego.
To tyle, jeśli chodzi o najcięższe elementy głośnika, a teraz wrócę do tematu uszkodzeń cewek.
Jeśli poprawnie wykonany obwód współpracuje z dobrej klasy koszem i wysokość uzwojenia cewki dobrana jest optymalnie do grubości nabiegunnika, a mimo to ulega ona uszkodzeniu, to w takim wypadku należy przeanalizować sposób jej wykonania i użyte w procesie produkcji materiały. Przy czym przypominam, że nie omawiam w tym artykule uszkodzeń powstałych w wyniku błędów w użytkowaniu czy, dajmy na to, awarią wzmacniacza.
Wspominałem już w ubiegłym miesiącu o najlepszym materiale na karkasy cewek, czyli o włóknie szklanym, więc żeby się nie powtarzać podam tylko jako ciekawostkę, że po raz pierwszy takie cewki pojawiły się na rynku już w połowie lat 60. i nadal jest to jedyny materiał, który spełnia najbardziej surowe wymagania, co tylko potwierdza moją tezę o tym, że dobrych wzorców w produkcji głośników można szukać nawet kilkadziesiąt lat temu.
Inne materiały nie kwalifikują się w zasadzie do celów profesjonalnych, choć ta uwaga nie dotyczy głośników wysokotonowych, bo cewki driverów pracują jednak z mniejszymi obciążeniami prądowymi i mechanicznymi.
Jednak nawet wykonanie karkasu z włókna szklanego i nawinięcie uzwojeń dwustronnie nie pomoże, jeśli np. zastosuje się niewłaściwy klej, drut o słabej wytrzymałości termicznej izolacji, albo popełni się jakieś błędy w trakcie nawijania uzwojeń, co jest stosunkowo często spotykaną wadą w wielu głośnikach wykonywanych na zautomatyzowanych liniach produkcyjnych. Na załączonej fotografii pokazuję taką firmową, dwustronną cewkę, która uległa spaleniu, a część uzwojeń pozostała w szczelinie.
Warto wiedzieć, że w warunkach przemysłowych firmy często używają drutów nawojowych samospiekających się, czyli takich, w których spajanie uzwojeń pokrytych specjalnym klejem następuje na skutek przepuszczania przez cewkę dużego prądu w krótkim czasie. Metoda szybka i wygodna dla fabryki, ale mająca kilka wad, których unika się, gdy cały karkas cewki wraz z nawiniętym uzwojeniem poddajemy działaniu wysokiej temperatury, która powoduje utwardzenie kleju i sprawia, że jego wytrzymałość w następstwie tego procesu jest znacznie wyższa, niż wytrzymałość termiczna izolacji drutu nawojowego.
Podam dla przykładu, że wszystkie cewki mojej produkcji, nawijane oczywiście wyłącznie na włóknie szklanym, wygrzewane są w procesie montażu do momentu, gdy temperatura powierzchni uzwojeń osiągnie ok. 200 stopni, a ponieważ nagrzewana jest aluminiowa oprawka, na której znajduje się karkas, to ciepło przenika przez całą strukturę cewki, a uzwojenia na czas wygrzewania są jeszcze dodatkowo dociskane do karkasu przy użyciu metody, która nigdy nie znalazłaby zastosowania w fabryce, choćby ze względu na jej pracochłonność.
Taka technologia powoduje, że drut nawojowy niejako „wciskany” jest na gorąco w karkas (w przypadku cewki nawijanej dwustronnie w jego wewnętrzną i zewnętrzną warstwę), a cewka po ostygnięciu i zdjęciu z oprawki, na której była nawijana, stanowi sztywny, niepodatny na odkształcenia „monolit” i jest niemal niezniszczalna, wyjąwszy oczywiście sytuacje ekstremalne.
Istotną zaletą tak wykonanej cewki jest również to, że uzwojenia nie tylko wyjątkowo silnie łączą się między sobą, ale – co jest równie ważne – są bardzo trwale związane z karkasem, dzięki czemu zazwyczaj nie zsuwają się z niego, nawet w przypadku całkowitego ich spalenia (zwęglenia). Oczywiście w takim wypadku karkas pozostaje nietknięty, gdyż odporność termiczna włókna szklanego jest większa niż najwyższe temperatury, jakie mogą wydzielić się w cewce, nawet w trakcie „pożaru” uzwojeń. Tyle że „wyprodukowanie” takiej cewki, nie licząc samego wykonania karkasu, zajmuje mi godzinę, a nawet więcej w przypadku cewek dużej mocy o największych średnicach, na co z pewnością nie mógłby sobie pozwolić żaden duży producent. Tym bardziej że opisanych procesów technologicznych raczej nie da się zautomatyzować, więc mogą być wykorzystywane wyłącznie przez hobbistów i pasjonatów, do których sam również się zaliczam.
Na kolejnej fotografii widoczna jest cewka nawinięta na kaptonie, której uzwojenia na skutek błędu technologicznego po prostu się rozeszły i częściowo zsunęły z karkasu, co spowodowało zatarcie cewki w szczelinie, i głośnik wymagał naprawy. To stosunkowo często spotykana wada fabryczna głośników niższej klasy i głośników, które były już naprawiane przez domorosłych „fachowców”.
Słabość technologii drutów samospiekających się widać tutaj jak na dłoni, bo uzwojenie w zasadzie można bez specjalnego wysiłku zsunąć z karkasu, a to dlatego, że klej połączył jako tako jedynie uzwojenia między sobą, ale miedzi do karkasu już nie za bardzo. Jest to klasyczny przykład „chałtury” głośnikowej, gdy znany producent aparatury firmuje swoją naklejką produkt wykonywany gdzieś na Dalekim Wschodzie, który chluby mu nie przynosi.
Jeszcze jedną słabością karkasów wykonywanych z tworzyw sztucznych jest ich mała sztywność, co ma szczególnie istotne znaczenie przy cewkach o dużej średnicy i wysokości. Na fotografii pokazuję, jak łatwo jest ugiąć taki karkas, przykładając do niego nawet niewielką siłę, co jest zupełnie niemożliwe w przypadku wykorzystania włókna szklanego, choć grubość takiego karkasu jest również bardzo niewielka (0,15 mm w przypadku wszystkich wyrobów PMP).
Oczywiście cewki wykonywane przez wiodących producentów branżowych spełniają większość wymagań, o których wspominam, ale pojawiają się inne problemy, które powodują, że głośnik ulega awarii. Można tutaj np. wspomnieć o uszkodzeniach na styku wyprowadzeń drutu nawojowego cewki i elastycznej linki łączącej końce uzwojeń z zaciskami głośnika. Jest to stosunkowo często spotykana awaria, będąca ewidentną wadą technologiczną, która jest o tyle przykra dla użytkownika, że pozornie nieuszkodzony głośnik odmawia posłuszeństwa, a amatorskie próby jego naprawienia zazwyczaj są skuteczne tylko na krótką metę, bo nie powodują usunięcia prawdziwej istoty problemu.
Kolejną przyczyną uszkodzeń może być odklejenie się cewki od membrany, najczęściej na skutek niestarannego montażu albo z powodu zastosowania niewłaściwego kleju. Amatorskie próby naprawiania tak uszkodzonych głośników często wzbudzają jedynie uśmiech politowania, choć z drugiej strony jest to jedna z tych awarii, które kompromitują producenta i nigdy nie powinny mieć miejsca w sprzęcie nie tylko profesjonalnym.
Prawidłowo wklejona cewka powinna być na tyle mocno połączona z membraną, żeby jej demontaż był zupełnie niemożliwy, a jego ewentualne próby muszą skutkować uszkodzeniem. Aby trwale połączyć cewkę z membraną, należy stosować odpowiednie kleje, które nie tylko łączą papier i materiał karkasu powierzchniowo, ale również wnikają w strukturę obu tych materiałów. Tyle że taki klej może być np. 20 x droższy od innego, popularnego spoiwa, co przy produkcji masowej ma niebagatelne znaczenie. Obecnie wiele firm wykorzystuje kleje „ekologiczne” albo kleje silikonowe, co po pierwsze utrudnia wszelkie naprawy, bo takie spoiny nie poddają się działaniu rozpuszczalników, a po drugie, jakość tak wykonanych połączeń czasem pozostawia sporo do życzenia.
Cewkę można również „na upartego” wkleić w taki sposób, że nie znajdzie się ona dokładnie w osi otworu membrany i nie zachowa położenia idealnie prostopadłego do zawieszeń, co może w skrajnych wypadkach powodować, że głośnik jest niesprawny od nowości albo ulega uszkodzeniu na pierwszej imprezie. Można również popełnić błąd polegający na tym, że cewka co prawda jest wklejona osiowo i prostopadle do krawędzi membrany, ale wyżej lub niżej niż powinna, czyli tak, żeby uzwojenie znajdowało się dokładnie pośrodku nabiegunnika. W efekcie takiego błędu głośnik będzie pracował z dużymi zniekształceniami przy ruchu w jedną ze stron, a przy większej mocy i amplitudzie uzwojenia cewki, których nie obejmie pole magnetyczne, po prostu ulegną uszkodzeniu.
Opisane awarie mogą mieć miejsce zarówno w głośnikach „prosto z fabryki”, jak i remontowanych przez pseudofachowców, i jeśli chodzi o ten ostatni przypadek, to wspomnę tylko, że czasem łapię się za głowę, gdy trafiają do mnie głośniki naprawiane przez osoby, które zdecydowanie nie powinny zajmować się tym rzemiosłem. Jednak z jakichś powodów to robią i w efekcie takich działań głośniki nigdy nie odzyskują pełnej sprawności, a często bywa tak, że zostają uszkodzone jeszcze bardziej. Jako przykład niech posłuży fotografia, na której widać, jak „naprawiacz” w miejsce fabrycznie stosowanego karkasu z dobrej klasy kaptonu zastosował zamiennie karkas z aluminium, na który nawinął uzwojenie w taki sposób, że po krótkim czasie po naprawie zsunęło się z niego i w całości utkwiło w szczelinie obwodu. Czasami trzeba dużo cierpliwości i wprawy, żeby je stamtąd wydostać, ale jeśli się to nie uda, to głośnik można już tylko spisać na straty.
Bywa nawet tak, że głośniki próbują naprawiać osobiście ich właściciele, co przy braku wiedzy i doświadczenia przynosi zazwyczaj opłakane rezultaty, że o niepotrzebnie poniesionych kosztach nie wspomnę. Nie chcę tutaj jednak rozwijać tematu serwisowania głośników, który obszernie omawiam na mojej stronie internetowej, w zakładce poświęconej ich naprawom, i każdy, kto jest zainteresowany bardziej szczegółowymi informacjami, może się z nimi tam zapoznać.
Teraz wypada poświęcić trochę miejsca membranom i zawieszeniom, bo również są to elementy mające duże znaczenie dla niezawodności i poprawnej pracy głośników. Ponieważ posiadam własną technologię wytwarzania wyżej wymienionych podzespołów, nieskromnie uważam się za osobę bardzo kompetentną w tym temacie i jestem w stanie bez trudu „organoleptycznie” ocenić jakość głośnika, rozpatrywaną właśnie pod tym kątem. Był czas, gdy duża liczba czołowych producentów głośników, szczególnie angielskich, zaopatrywała się w te podzespoły w jednej fabryce, która istnieje już ponad 80 lat i nadal produkuje je przy użyciu maszyn i technologii, które pamiętają niekiedy czasy, gdy Beatlesi byli dopiero obiecującym, młodym zespołem. Ponieważ jednak jest to firma europejska, jej produkty są wielokrotnie droższe od „chińszczyzny”, i niektóre firmy, tnąc koszty, zdecydowały się na zmianę dostawcy, czego potem mocno żałowały. Wykonanie dobrej, trwałej membrany papierowej (bo tylko o takich będę pisał) nie jest sprawą prostą i dotyczy to także zawieszeń, zwanych również resorami. Po pierwsze, należy zastosować właściwy rodzaj celulozy, a tylko niektóre, nieliczne jej gatunki nadają się do tego celu. Po drugie, należy membranie nadać właściwy do danej aplikacji kształt, w procesie tłoczenia w specjalnych formach.
Oczywiście każda membrana wymaga własnego oprzyrządowania, czyli stempla i matrycy, co przy większej ich liczbie i dużych gabarytach membran generuje ogromne koszty wykonania form, które muszą być precyzyjnie wytoczone z metalu. Po trzecie, gdy membrana zostanie już wytłoczona w procesie formowania wodnego roztworu celulozy, należy ją zaimpregnować specjalnymi preparatami chemicznymi i następnie dokleić górne zawieszenie, wykonywane dokładnie w ten sam sposób, czyli przy użyciu stempla i matrycy. Zawieszenie z kolei wymaga zastosowania odpowiedniej tkaniny i następnie musi być również impregnowane przy użyciu preparatu, przy którym woń kleju Butapren może wydać się zapachem fiołków.
Membrana jest elementem narażonym na duży „stres” mechaniczny i dlatego tak ważne jest, aby była wykonana poprawnie i z odpowiednich materiałów. W przeciwnym razie może albo ulec odkształceniu, co nieuchronnie prowadzi do uszkodzenia cewki na skutek utraty centrowania, albo może nawet przełamywać się (pękać) w określonych miejscach, czyli przeważnie tam, gdzie występują największe naprężenia. Bywa również, że membrana ulega rozwarstwieniu, co jest już skrajnym przykładem jej kiepskiej jakości, ale z takimi przypadkami też się spotykałem.
W mojej praktyce serwisowej kiepska jakość membran i resorów stanowi wcale nie mniejszą przyczynę uszkodzeń głośników niż awarie cewek, które niekiedy są całkowicie sprawne i wyglądają jak nowe, również w głośnikach pochodzących z czasów, gdy wielu czytelników pisma Live Sound nie było jeszcze na świecie. Na fotografii widoczna jest właśnie taka nieuszkodzona cewka, bardzo przyzwoicie wykonana, ale destrukcji uległa kiepska membrana, której jakość jest dużo gorsza od cewki.
Dodam przy okazji, że próby naprawy tak uszkodzonych głośników poprzez wycinanie sprawnych cewek i wklejanie ich do nowych, często zupełnie przypadkowo dobranych membran to klasyczny przykład amatorszczyzny, podobnie zresztą jak sytuacja odwrotna, bo tylko całkowita wymiana całego układu drgającego przywraca głośnikowi jego pierwotne parametry, a czasem nawet je poprawia, o ile zastosuje się komponenty lepszej klasy niż oryginalne.
Ważne jest również, żeby w miejscu, gdzie wklejana jest cewka, membrana miała odpowiednią grubość, a co za tym idzie – sztywność, bo w przeciwnym razie nie da się w niej poprawnie zamocować karkasu cewki. Oczywiście zupełnie inaczej będzie wykonana membrana głośnika gitarowego, a inaczej przetwornika niskotonowego dużej mocy, choć proces produkcyjny przebiega praktycznie w ten sam sposób. Różnica polega również na tym, że głośniki gitarowe (ale nie do gitary basowej) nie mają oddzielnego, górnego zawieszenia z tkaniny, bo jego rolę spełniają odpowiednie przetłoczenia w materiale, z którego wykonana jest sama membrana. Takie zawieszenie określane jest w terminologii angielskiej mianem PE (paper edge), w przeciwieństwie do wersji z tkaniny, czyli CE (cloth edge). Zawieszenie PE siłą rzeczy jest mniej trwałe i podobna sytuacja jest z resorami wykonywanymi z pianki poliuretanowej, która z upływem czasu starzeje się i kruszy, co jest bolączką wielu głośników stosowanych w aparaturze Hi-Fi, no ale to zupełnie inna działka, którą ja się nie zajmuję.
Jeśli chodzi o resory, to wielokrotnie w mojej praktyce serwisowej miałem do czynienia z sytuacją, gdy nawet fabrycznie nowy głośnik, wyposażony w stosunkowo niezłą membranę, dyskwalifikowały właśnie kiepskiej jakości zawieszenia, i to zarówno górne, jak i dolne. Zbyt mała sztywność tych elementów powoduje, że membrana przy większych mocach wykonuje ruchy o zbyt dużej amplitudzie i jej drgania są kiepsko tłumione, co prędzej czy później musi powodować destrukcję głośnika. Niesłychanie ważny jest również kształt i wysokość fałd resorów i sposób impregnacji tych elementów po wytłoczeniu, ale także po finalnym zmontowaniu głośnika. Firmy stosują różne „patenty” mające na celu poprawę właściwości mechanicznych zawieszeń, począwszy od pokrywania ich różnymi preparatami, a skończywszy na sklejaniu kilku resorów, i zanotowany przeze mnie „rekord” w tej dziedzinie to 5 dolnych resorów sklejonych ze sobą, czego komentować nie będę, bo nie warto zajmować się głośnikową „pornografią”.
Recepta na dobre zawieszenie jest prosta: właściwa tkanina, optymalny dla danej aplikacji kształt, poprawna technologia tłoczenia i na końcu odpowiednia impregnacja. Oczywiście to tylko pozornie prosta recepta, czego najlepszym dowodem jest to, że wiele głośników już na „dzień dobry” dyskwalifikują właśnie kiepskiej jakości zawieszenia. Amatorskie próby „reanimacji” resorów, które utraciły swoje pierwotne właściwości, kończą się czasem ich całkowitym zniszczeniem, gdy np. domorosły specjalista pokryje je czymś w rodzaju lepiku asfaltowego, więc zdecydowanie odradzam podobne praktyki.
Na fotografii pokazuję resory wytwarzane we własnym zakresie przez firmę PMP, choć nie obejmuje ona całego asortymentu tych elementów.
Widoczne są również na niej kołpaki osłonowe cewek dostosowane do ich różnych średnic, które w przypadku wersji papierowej (a nie materiałowej) dodatkowo usztywniają dolną część membrany i pomagają w chłodzeniu cewki, przetłaczając powietrze przez szczelinę magnetyczną. W prawym górnym rogu zdjęcia pokazuję także tubki papierowe, stosowane dawniej dość powszechnie w celu rozszerzenia górnego pasma przenoszenia głośników, które w takim wykonaniu określane są jako wersja TC (Twin Cone).
W uzupełnieniu tematu serwisowania uszkodzonych głośników dodam jeszcze, że w mojej pracowni przeprowadzam wyłącznie pełną regenerację głośników dostarczonych do naprawy, czyli pozbawiam je wszystkich fabrycznych elementów ruchomych i następnie, po dokładnym oczyszczeniu koszy i szczelin obwodów magnetycznych, montuję przygotowany w firmie komplet naprawczy, wykonany wyłącznie z podzespołów własnej produkcji.
Niektóre ze zdemontowanych cewek i membran zachowuję jako „świadectwo historii” i kunsztu producenta, a inne przechowuję tylko w celu demonstracji, jak nie należy ich wykonywać. Większość starych elementów trafia jednak do śmietnika i wyglądają po demontażu tak, jak na zdjęciu otwierającym ten artykuł.
Informuję, że wszystkie zdjęcia zamieszczone w tekście są mojego autorstwa, w przeciwieństwie do materiałów fotograficznych w pierwszej części artykułu, które pochodziły od redakcji.
A na zakończenie jeszcze raz zapraszam na moją stronę firmową, gdzie w zakładkach „Głośniki PMP” i „Naprawa głośników” można poszerzyć swoją wiedzę na temat technologii głośnikowych, którą – w mocno skondensowanej formie – starałem się przekazać czytelnikom Live Sound w tym i w poprzednim numerze miesięcznika.
Piotr Peto