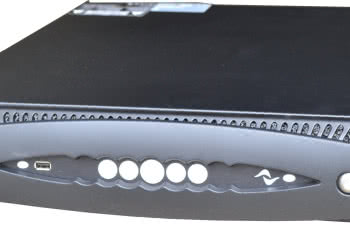
X4L - wzmacniacz z DSP z serii X
Biznes „nagłośnieniowy” – w porównaniu z innymi dziedzinami techniki (np. przemysłem samochodowym, czy ...
Stare i znane powiedzenie mówi, że każdy łańcuch jest tak mocny, jak jego najsłabsze ogniwo. I nie da się temu zaprzeczyć, jednak każde urządzenie składa się z elementów mniej lub bardziej istotnych dla właściwej pracy, do jakiej owo urządzenie jest przeznaczone.
W samochodzie do najbardziej istotnych elementów zaliczymy zapewne silnik i hamulce, zaś mniej ważne będą np. klimatyzacja czy skórzane fotele. Wróćmy jednak na „nasz” grunt. Jak jest zbudowany klasyczny głośnik dynamiczny, chyba każdy czytelnik LSI mniej więcej się orientuje – jest kosz, magnes, cewka, membrana i jej zawieszenia, muszą być też jakieś konektory i przewody łączące je z cewką. O ile kosz jest ważny bardziej w kontekście parametrów mechanicznych (i wagi), o tyle magnes, membrana i cewka – tworząc w zasadzie nieodłączny układ – mają przede wszystkim wpływ na walory akustyczne, czyli brzmieniowe, głośnika. A przecież to właśnie właściwości „przetwórcze”, skutkujące takim czy innym brzmieniem, są najważniejszym (no, nie dla wszystkich, niektórzy przede wszystkim – niestety – patrzą na cenę) kryterium doboru danego przetwornika do urządzenia głośnikowego. Skoro układ magnes- cewka-membrana jest taki kluczowy, przyjrzyjmy się mu bliżej i zobaczmy jak parametry tych elementów wpływają na finalne brzmienie głośnika.
Na początek
Na przewód znajdujący się w polu magnetycznym, przez który przepływa prąd elektryczny, działa siła. Dla danej wartości prądu i pola magnetycznego będzie ona największa, kiedy kierunek przepływu prądu będzie prostopadły do linii pola magnetycznego. W głośniku dynamicznym cewka jest umieszczona w szczelinie powietrznej w obwodzie magnetycznym. Pole magnetyczne jest zorientowane promieniowo, to znaczy, że działa poprzecznie do szczeliny, rozchodząc się promieniście. Jak można zobaczyć na rysunku na sąsiedniej stronie, oznacza to, że prąd jest prostopadły do pola magnetycznego (niebieskie strzałki) w szczelinie.
Indukowana siła jest również proporcjonalna do wartości pola magnetycznego, prądu i długości przewodu w szczelinie. Dla danego magnesu im szersza szczelina powietrzna, tym mniejsza będzie w niej „siła” (indukcja) pola magnetycznego. Tak więc wąskie szczeliny dostarczają najsilniejsze pole, ale cewka musi się w niej mieścić, i to z odpowiednią tolerancją, by uchronić się od ocierania o brzegi magnesu w czasie ruchu. Dla danej wielkości przewodu im jest on dłuższy (im więcej miejsca zajmuje w szczelinie wzdłuż jej długości), tym cieńsza cewka i tym większa rezystancja, co wpływa na redukcję wartości prądu. Używając grubszych przewodów zmniejszamy rezystancję, ale zwiększamy grubość cewki i jej masę, wymagając szerszej szczeliny, przez co obniżamy wartość indukcji magnetycznej.
Większość głośników niskotonowych używanych w profesjonalnych aplikacjach nagłośnieniowych wykorzystuje cewki o większej długości, niż długość szczeliny powietrznej. Sprawia to, że podczas wychylania cewki cały czas wypełnia ona całą długość szczeliny, pod warunkiem że nie wychyli się ona nigdy tak daleko, aby jej końce schowały się we wnętrzu szczeliny. Jeśli się to zdarzy, efektywna długość przewodu poddanego działaniu pola magnetycznego zmniejszy się, co zredukuje wielkość działającej na cewkę siły indukcji.
Niektóre z pierwszych produkowanych głośników dynamicznych do wytworzenia pola magnetycznego wykorzystywały wypełnioną cewkę. Był to po prostu elektromagnes zrobiony z dużego zwoju kabla, nawiniętego dookoła kawałka magnesu i przenoszący prąd stały. Czasami takie wypełnione cewki były używane jako duży dławik, aby wyrównać napięcie we wzmacniaczu.
W latach 30. ubiegłego stulecia został wynaleziony nowy materiał magnetyczny zwany Alnico (stop aluminium, niklu i kobaltu) i od razu stał się popularnym materiałem wytwarzającym stałe pole magnetyczne. Alnico charakteryzował się dobrym stosunkiem energii do wagi, ale wojna domowa w Zairze w 1978 roku zamknęła jedyne komercyjne źródło kobaltu na świecie. Skutkiem tego było szybkie zastąpienie, w większości zastosowań, Alnico magnesami ferrytowymi.
Magnesy ferrytowe są ceramicznym materiałem zrobionym z żelaza oraz tlenku baru lub/i strontu. Są stosunkowo niedrogie, ale mają dość niski współczynnik energii do wagi, co oznacza, że głośnik z magnesem ferrytowym będzie zwykle cięższy niż taki sam, ale z magnesem alnico tej samej mocy.
Bardzo mocne, lekkie magnesy zrobione z neodymu, żelaza, boru i małych ilości kilku różnych składników były najpierw opatentowane przez Sumitomo, General Motors i Chińską Akademię Nauk w 1983 roku. Magnesy neodymowa są, jak na ich wagę, „straszliwie mocne”, ale pierwsze ich formy traciły swój magnetyzm w wystarczająco wysokich temperaturach, będąc problemem dla głośników zasilanych dużą mocą. W późniejszych latach wprowadzono ulepszenia do magnesów neodymowych, aż do zwiększenia ich mocy i rezystancji w wysokich temperaturach. Z powodu tych ulepszeń i wysokiego współczynnika energii do wagi „neo” stały się bardziej popularne w głośnikach około roku 2000. Popularność głośników noedymowych wciąż rośnie, jednak wzrastająca cena neodymu i innych komponentów spowodowała ostatnio spory niepokój i po dość znaczących podwyżkach tychże głośników zauważa się powrót do „starych, dobrych” ferrytów.
Z uwagi na to że cewka jest przeznaczona do przewodzenia prądu elektrycznego, powinna być zrobiona z materiału o wysokiej przewodności. Najbardziej popularnymi materiałami na przewodniki są miedź i aluminium. Właściwie to srebro jest materiałem o najwyższej przewodności elektrycznej, ale jest zbyt drogie, aby być praktycznym w takich zastosowaniach, jak cewki głośnikowe. Aluminium ma niższą przewodność niż miedź (porównując objętość), ale wyższą wagowo, więc jest często używane, kiedy ważne jest utrzymanie minimalnej wagi cewki. Kilku producentów głośników wykorzystuje czyste aluminium, ale materiał ten dość łatwo wchodzi w relacje z tlenem, tworząc powłokę prawie natychmiast przy zetknięciu z powietrzem. Tlenki tworzące taką powłokę mogą być właściwie wykorzystane jako izolacja, zamiast pokrywania przewodów emalią, ale jednocześnie utrudniają prawidłowe lutowanie połączeń. Z tych powodów wielu producentów używa aluminiowe przewody pokryte miedzią, które są tylko troszkę cięższe niż czysto aluminiowe i z którymi pracuje się o wiele prościej.
Najbardziej popularna konstrukcja znana jest jako cewka dwuwarstwowa. W tej konstrukcji przewód (zwykle okrągły w przekroju) jest nawinięty na cylindryczny papier lub plastikowy karkas, zaczynając się na górze i zniżając spiralnie do samego dołu cewki. Tam jest to odwrócone i druga warstwa jest nawinięta na pierwszej, wracając do góry. Jedną z dużych zalet tego typu konstrukcji jest to, że wyprowadzenia są zostawione u góry tego zwoju. Przewody otulają karkas, a podłączone są do elastycznej plecionki drucianej z materiału przewodzącego, która przewodzi prąd do końcówek przyłączeniowych zamontowanych na koszu głośnika.
Czterowarstwowa cewka jest taka sama, jak dwuwarstwowa z wyjątkiem tego, że nawinięte są dwie warstwy więcej, w dół i z powrotem do góry po raz drugi. Oczywiście możliwe jest nawinięcie jakiejkolwiek liczby warstw w ten sposób, ale rzadko spotyka się więcej niż cztery. Czterowarstwowa cewka normalnie byłaby wykorzystana w głośniku niskotonowym lub subwooferze, gdzie większa masa cewki nie jest szkodliwa. Miedź to najpowszechniejszy przewodnik wykorzystywany w cewkach dwu- i czterowarstwowych, zaś w przypadku konieczności zmniejszenia masy cewki wykorzystuje się aluminium powleczone miedzią i czyste aluminium.
Jakakolwiek cewka nawinięta okrągłym drutem będzie miała przestrzenie powietrzne pomiędzy zwojami drutu. Dla danego drutu powierzchnia przekroju poprzecznego i liczba warstw zwiększa grubość cewki. Kwadratowy lub prostokątny przekrój poprzeczny drutu może wyeliminować te przestrzenie, przez co zmniejszyć grubość cewki, pozwalając na węższe szczeliny powietrzne i większą indukcję pola magnetycznego. Jednakże te zalety okupione są większą trudnością w wytworzeniu takiej cewki. Większość cewek tego typu wykorzystuje jedną warstwę drutu prostokątnego, ze zwojami stykającymi ze sobą szerszymi krawędziami (a więc nawija się je krawędzią węższą na karkasie), które często nazywane są cewkami „edgewound” (po polsku, zamiast tego jednego słowa, musielibyśmy użyć określenia „cewka z nawinięciem krawędziowym”). W cewkach jednowarstwowych jeden koniec drutu pozostawiony jest na dole zwoju i zwykle prowadzony do góry w środku cewki, w rowku w biegnącym w karkasie. Cewka „edgewound”, ze względu na swoją grubość porównywalną z cewkami wielowarstwowymi, będzie zwykle sztywniejsza z uwagi na zwiększoną powierzchnię przylegania zwojów. Z powodu stosunkowo wysokich kosztów cewki „edgewound” używane są tylko wtedy, kiedy najistotniejsze są duża indukcja pola magnetycznego i mała masa, tak jak w głośniku ciśnieniowym, i dlatego zwykle są one aluminiowe lub aluminiowe z miedzianą powłoką.
Chociaż karkas jako taki nie bierze udziału w wytwarzaniu siły napędowej głośnika, musi tę siłę przenosić do membrany lub kopułki, z wyjątkiem rzadkiego przypadku przetwornika bezkarkasowego, gdzie cewka jest przymocowana bezpośrednio do membrany. Materiały na karkas wybierane są tak, aby brać pod uwagę kombinację takich parametrów jak: masa, sztywność i charakterystyki cieplne. Papier ma dobry współczynnik masy do sztywności i jest bardzo niedrogi, ale nie może być używany w aplikacjach dużej mocy, ponieważ kiepsko radzi sobie z odprowadzaniem ciepła. Jest zwykle wykorzystywany w głośnikach małej lub średniej mocy, stosowanych w piecach gitarowych, z powodu swoich mile widzianych charakterystyk akustycznych. Nomex jest materiałem syntetycznym papieropodobnym, który może absorbować więcej ciepła i jest nieco droższy niż papier. Bardzo odpornym na działanie temperatury jest polimer, i jest on bardzo popularny w produkcji karkasów z powodu dużego współczynnika sztywności do masy i możliwości wytrzymania temperatury wyższej niż 350°C. Aluminium to kolejny materiał, z którego wytwarza się karkasy, mogący wytrzymać bardzo wysokie temperatury, ale w kilku przypadkach jego wysoka przewodność cieplna może przenieść te wysokie temperatury do membrany i środków klejących, używanych we wszystkich membranach/cewkach. Następnym materiałem jest włókno szklane, wykorzystywane czasami jako materiał do produkcji karkasów.
Dźwięk to nic innego jak drgania cząstek powietrza, a percepcja tych drgań polega na ich interpretacji przez nasze uszy i mózg. Aby wytworzyć drgania cząstek powietrza, musimy dysponować czymś, co będzie je wprawiać w ruch, poprzez wykonywanie ruchu drgającego. Wyjaśnimy sobie więc kilka spraw dotyczących form stosowanych obecnie membran, materiałów, z jakich są one wykonane, i dlaczego akurat takich, a nie innych.
Na powierzchni naszej planety żyjemy zanurzeni w oceanie powietrza, które jest mieszaniną cząstek różnych gazów, głównie azotu (78%), tlenu (21%), argonu, pary wodnej i śladowych ilości innych gazów. Wydawać by się mogło, że powietrze nie ma masy – nic bardziej błędnego, metr sześcienny powietrza waży ok. 1,2 kg.
Skoro powietrze ma pewną masę, będziemy potrzebować odpowiedniej siły, aby nim poruszać. Jeśli mamy sporo tego powietrza (np. gdy chcemy wytworzyć głośny dźwięk) i chcemy to zrobić efektywnie, będziemy potrzebować czegoś solidnego, o dużej powierzchni, a jednocześnie lekkiego. Ponadto taka membrana musi też mieć odpowiednią sztywność, aby nie wyginać się pod obciążeniem. Dlatego tak istotnym parametrem jest stosunek sztywności do masy. Nie ma takiego materiału, dla którego ten parametr miałby wartość równą nieskończoności, tak więc pewne deformacje są nieuniknione i wszystkie membrany będą podlegały podziałowi na pewne mody rezonansowe, w zależności od częstotliwości. Na nasze nieszczęście wiele materiałów charakteryzujących się wysokim stosunkiem sztywności do masy ma relatywnie niskie tłumienie wewnętrzne (tarcie wewnętrzne), wywołując tendencje do „dzwonienia” przy pewnych częstotliwościach. To jest powodem tego, że dzwony i kamertony widełkowe robi się z metalu. Dzwonienie to nie jest problemem tylko wtedy, kiedy występuje poza użytecznym pasmem częstotliwości pracy głośnika.
Materiały charakteryzują się pewną własnością zwaną modułem Younga, dzięki której w sposób mierzalny możemy określić ich sztywność. Jednak sztywność konkretnego produktu, wykonanego z materiału o znanej wartości modułu Younga, zależy również od jego kształtu. Płaska płytka nie będzie tak sztywna, jak stożek, stąd taka popularność obecnie stosowanych głośnikowych membran stożkowych. Te zaś z kolei można podzielić na membrany o prostych lub zakrzywionych ściankach. Z powodu takiego kształtu membrany o zakrzywionych ściankach ulegają podziałowi rezonansowemu przy wyższych częstotliwościach niż membrany o ściankach prostych o takich samych wymiarach i masach. Dzięki temu te pierwsze charakteryzują się bardziej płaską i gładką charakterystyką częstotliwościową. Membrany o prostych ścianka przeważnie mają wcięcie, a następnie podbicie na charakterystyce częstotliwościowej, odpowiadające pierwszemu modowi podziału rezonansowemu membrany.
Membrany głośnikowe przeważnie zbudowane są z dwóch składników. „Korpus” jest to część wyprofilowana stożkowo, która z założenia powinna być tak sztywna, jak to jest tylko możliwe. „Resor” jest przeważnie pofalowany i miększy niż korpus, aby mógł się uginać, pozwalając poruszać się korpusowi. Papier jest bodajże jedynym materiałem używanym do produkcji membran zarówno 30 lat temu, jak i dzisiaj. Większość z pierwszych membran oraz wiele współczesnych jest całkowicie papierowymi konstrukcjami, włączając w to również resor. Równie popularnymi materiałami, z których wykonywano resory membran, były skóra i filc. Współcześnie produkowane membrany wykonywane są z bardzo wielu różnych materiałów.
Wciąż bardzo popularnym materiałem wykorzystywanym obecnie do produkcji membran jest papier. Wydawałoby się, że to bardzo proste rozwiązanie w naszym wysoko uprzemysłowionym świecie, ale papier jest naprawdę bardzo dobrym materiałem na membrany z kilku powodów. Charakteryzuje się dobrym stosunkiem sztywności do masy, ma naturalnie wysokie tłumienie wewnętrzne, no i (co ważne) jest tani. Pierwsze membrany papierowe oraz niektóre wciąż używane w głośnikach gitarowych wycinane były z arkusza papieru w kształt kawałka pizzy z brakującym kawałkiem, a następnie zwijane w stożek i sklejane wzdłuż zakładki. Obecne membrany papierowe są wyprasowywane lub modelowane (odsysane) z masy papierowej na sitach stożkowych, a następnie suszone.
Masę papierową sporządza się z zawiesiny włókien celulozowych w wodzie z dodatkiem impregnatu będącego mieszaniną siarczanu miedzi z mydłem i mleka kauczukowego. Masę, po dokładnym wymieszaniu, podaje się na sito o kształcie i rozmiarach membrany. Za pomocą pompy próżniowej odsysa się wodę, a następnie sito z pozostałą na nim masą, po sprawdzeniu jednolitości warstwy, poddaje się suszeniu.
Różne metody suszenia mają istotny wpływ na własności produktu finalnego. Suszenie w matrycy polega na ściskaniu masy papierowej pomiędzy gorącymi metalowymi matrycami i sprasowaniu, w efekcie czego otrzymujemy twardy i zbity korpus. W metodzie transferowej korpus jest przenoszony z sita modelującego na inne sito, gdzie przepływające przezeń gorące powietrze suszy go. W tej metodzie membrana również podlega pewnemu sprasowaniu, jednak nie w takim stopniu jak w metodzie matrycowej, w rezultacie czego uzyskujemy średnią gęstość i twardość. W metodzie beztransferowej gorące powietrze jest przepuszczane przez korpus, gdy pozostaje on wciąż na sicie modelującym, co skutkuje powstaniem miększego i mniej gęstego korpusu. Tył membrany suszonej metoda beztransferową jest często chropowaty, ponieważ nigdy nie podlega prasowaniu.
Zarówno membrany klejone, jak i modelowane pokrywa się przeważnie powłoką lakierową, aby związać włókna celulozowe i uodpornić membranę na działanie wilgoci. Niezależnie od tego jak zostały wykonane, receptura proporcji włókien i żywic może być wykorzystana do kształtowania fizycznych własności wytworzonego papieru: od miękkiego do twardego jak drewno. Lakierowane membrany papierowe nie są też całkowicie wolne od działania wilgoci, toteż kontrolowanie konsystencji papieru w procesie wytwarzania jest zarówno sztuką, jak i nauką.
Tworzywa sztuczne, np. polipropylen, są prawdopodobnie drugie w kolejności popularności jako materiały na membrany. Często mają dodatki poprawiające ich stosunek sztywności do masy. Mogą być wytwarzane poprzez wyciskanie (formowanie) z arkuszy lub wtryskiwane w formy. Proces produkcji tych membran jest stosunkowo tani – co przekłada się na ich niską cenę – a same membrany mogą być mniej lub bardziej odporne na działanie wilgoci, jednak nie mogą konkurować z papierem pod względem stosunku sztywności do masy i elastyczności (łatwości w modelowaniu).
Aluminium i magnez są z powodzeniem stosowane do wytwarzania membran głośnikowych, jednak ich projektanci muszą zachować dużą ostrożność i być pewnymi, że pierwszy mod rezonansowy membrany wypadnie grubo powyżej użytecznego zakresu jej pracy. Z powodu bardzo małego tłumienia wewnętrznego rezonans membrany jest bardzo niepożądany. Membrany metalowe są przeważnie wykonywane za pomocą zwijania lub w procesie hydroformowania.
Włókna węglowe są jednym z najmocniejszych w swojej kategorii „wagowej” materiałem znanym człowiekowi. Używane są w membranach głośnikowych w różnorakich formach, jednak chyba najpopularniejszą jest tkanina z włókien węglowych, w której materiał z włókien węglowych jest impregnowany żywicą epoksydową lub inną, i z której następnie jest formowany odpowiedni kształt.
Włókna kevlarowe i szklane również znajdują swoje zastosowanie w tej materii. Są bardzo mocne i lekkie, mając jednocześnie przyzwoite tłumienie wewnętrzne, aczkolwiek płacić trzeba za nie jak „za zboże”.
Przetworniki wysokotonowe, tweetery i drivery ciśnieniowe mają przeważnie membrany w kształcie czaszy (kopułki), najczęsciej wykonane z metalu lub tworzywa sztucznego. Z metali jednym z obecnie najpopularniejszych jest tytan. Aluminium ma nieco wyższy stosunek sztywności do masy niż tytan, jednak jest mniej odporne zmęczeniowo, co może prowadzić do uszkodzenia membrany.
Konstrukcje złożone (kanapkowe) membran i kopułek są najbardziej wyrafinowane technologicznie. Do ich wytwarzania wykorzystuje się całą masę materiałów, między innymi plastikowe, metalowe („plastry miodu”) i piankowe rdzenie pokryte papierem, plastikiem, metalem lub impregnowanymi włóknami. Stosunek sztywności do masy i tłumienie wewnętrzne membran wykonanych w konstrukcjach kanapkowych mogą być doskonałe, jednak ich koszt może sprawiać, że będą nieosiągalne dla wielu aplikacji.
Resory membran są często wykonane z tkaniny fenolowej, która poddana jest wprasowaniu we właściwy kształt w gorącej metalowej formie. Równie często stosuje się piankę lub gumę. Resory piankowe przeważnie wykonuje się poprzez wprasowanie na gorąco arkusza pianki pomiędzy metalowymi matrycami, zaś resory gumowe wykonuje się poprzez wtryskiwanie lub formowanie tłoczne. Sporą część gumowych resorów wykonuje się z termoplastycznych elastomerów, takich jak Santoprene. Folie z tworzywa sztucznego, np. Mylar lub PET, wykorzystuje się powszechnie do wykonywania resorów membran głośników wysokotonowych. Resory wykonane z innego materiału niż korpus przeważnie formuje się, a następnie przykleja do membrany lub kopułki, aczkolwiek niektóre z elastomerów są natłoczone na korpus.
Wybór materiałów oraz kształtów membran jest bardzo szeroki. Projektant głośnika musi wybrać membranę o takim kształcie i wykonaną z takiego materiału, który spełni założenia projektowe pod względem zakresu przetwarzanych częstotliwości, efektywności, możliwie płaskiej charakterystyki i kosztów.
Jak widać, jest wiele dróg prowadzących do stworzenia odpowiednich głośników, tak aby otrzymać właściwą równowagę między siłą napędową, masą cewki, czystym, niezniekształconym brzmieniem w głośnikach dużej mocy, Xmax itp. Cała sztuka projektowania głośników polega na tym, aby dopasować te wszystkie różne opcje konstrukcji napędu z wyborem odpowiedniej membrany i innych komponentów, tak aby otrzymać zamierzony efekt.
Armand Szary