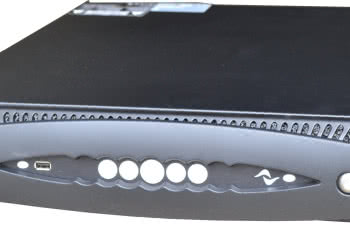
X4L - wzmacniacz z DSP z serii X
Biznes „nagłośnieniowy” – w porównaniu z innymi dziedzinami techniki (np. przemysłem samochodowym, czy ...
Nie od dziś wiadomo, że najwyższej klasy instrumenty muzyczne są wykonywane ręcznie przez zawodowych rzemieślników z wieloletnią praktyką oraz – zwykle – doskonałym słuchem, pozwalającym wychwycić najdrobniejsze brzmieniowe niuanse konstrukcji. I choć nowe technologie produkcji już dawno wkroczyły do branży muzycznej, to dopiero dziś wykonanie własnego instrumentu z niemal dowolnej grupy (dętego, strunowego, czy nawet perkusyjnego) jest możliwe w warunkach domowych, a nawet – co najciekawsze – bez dostępu do bogato wyposażonego warsztatu.
Wystarczy do tego celu dobry projekt, drukarka 3D z zapasem filamentu oraz klej i – ewentualnie – podstawowy osprzęt, którego (przynajmniej na razie…) nie sposób wydrukować z użyciem dostępnych technologii 3D. Internetowe „wykopaliska” na znanym wśród trójwymiarowych drukarzy portalu thingiverse.com pozwolą nam znaleźć niezwykle interesujące, proste w budowie, a co najważniejsze – sprawdzone w praktyce konstrukcje. Zapraszamy do przeglądu wybranych przez nas propozycji.
Naszą podróż po świecie drukowalnych instrumentów zaczniemy od najprostszych konstrukcji, które nie wymagają zbyt dużego nakładu pracy związanego z montażem czy też instalacją dodatkowego osprzętu. „Pierwszym z brzegu” przykładem jest okaryna – ten niewielki aerofon z powodzeniem daje się wydrukować z użyciem dowolnej drukarki 3D – jednym z lepiej dopracowanych projektów jest dostępny pod tym linkiem 12-otworowy instrument, opracowany przez zawodowego inżyniera ukrywającego się pod pseudonimem RobSoundtrack. Oryginalny model powstał z użyciem budżetowej, niezwykle popularnej drukarki 3D Creality CR-10. Co ciekawe, to niewielkie „cacko” osiąga naprawdę przyzwoite brzmienie, co może zaskakiwać, jeśli weźmie się pod pod uwagę technikę jego produkcji. Naturalną konsekwencją zastosowania druku 3D do tworzenia muzycznego arsenału jest powstanie szeregu prostych, ale w pełni funkcjonalnych akcesoriów, np. kapodasterów (tutaj dostępny jest projekt, w którym przemyślnie wykorzystano zasady projektowania elastycznych przegubów ze stosunkowo sztywnego materiału – PLA) czy też wieszaków do gitar (przykładowy projekt można znaleźć tutaj). Gitarzyści, którzy zmagają się z problemem ginących w niewyjaśnionych okolicznościach piórek, skorzystają z estetycznego i bardzo funkcjonalnego organizera do kostek gitarowych, dostępnego pod tym linkiem.
Okazuje się, że drukarkę 3D można wykorzystać także do stworzenia w pełni funkcjonalnych instrumentów strunowych. Na dobry początek można sięgnąć np. po ukulele. Pod tym linkiem dostępny jest projekt przetestowanego i co ważne – naprawdę przyjemnie brzmiącego (przynajmniej jak na instrument „plastikowy”) ukulele, wykonanego zaledwie z kilku połączonych ze sobą elementów. Ten sam autor pokusił się także o stworzenie niewielkiej gitary akustycznej w rozmiarze ¾, która co prawda mocno odbiega designem od klasycznego kształtu pudła rezonansowego, ale przynajmniej nie wymaga regulacji krzywizny gryfu – do montażu, oprócz drukowanych elementów, są potrzebne bowiem jedynie struny, maszynki i… klej, który posłuży do złączenia poszczególnych fragmentów pudła, gryfu oraz główki. Co ciekawe, druk nie wymaga stosowania podpór, co – przy niebagatelnych wymiarach elementów składowych instrumentu – znacznie oszczędza czas oraz użyty do produkcji filament. Znacznie dalej poszedł natomiast autor konstrukcji gitary elektrycznej, przedstawionej tutaj. Choć pod względem konfiguracji hadware’owej model nawiązuje do kultowego Stratocastera (projekt korzysta zresztą z klasycznego, drewnianego gryfu), to sam korpus zastąpiono ażurową konstrukcją, sklejoną z kilku wydrukowanych osobno elementów. Do produkcji tego nietypowego Strata użyto filamentu PLA, najpopularniejszego materiału wśród początkujących (i nie tylko) drukarzy 3D.
Odpowiedź na to pytanie jak zwykle zależy od oczekiwań muzyka, ale też jego pozamuzycznych pasji i zainteresowań. Osoby zafascynowane drukiem 3D z pewnością zechcą wykorzystać tę coraz popularniejszą technikę do stworzenia nietypowego, customowego instrumentu. Warto pamiętać, że nie zawsze konieczny będzie podział większych elementów (np. korpusów czy gryfów gitar) na sklejane po wydrukowaniu fragmenty. Na rynku istnieje bowiem wiele modeli drukarek o imponującej przestrzeni roboczej, które zdecydowanie ułatwią produkcję większych elementów. Przykładem mogą być najnowsze propozycje wspomnianego wcześniej, chińskiego producenta Creality – model Creality CR-10 Max udostępnia pole robocze o wymiarach aż 450 x 450 x 470 mm, a starszy Creality CR-10S5 aż 500 x 500 x 500 mm. Tak duży obszar roboczy niebywale zwiększa możliwości produkcyjne i – co ważne – ułatwia późniejszy montaż instrumentu. Zachęcamy do zapoznania się z ofertą sklepu dla robotyków Botland, w którym dostępne od ręki są nie tylko drukarki 3D i dedykowane do nich akcesoria, ale także bogaty wybór filamentów (w tym specjalne materiały na bazie proszku drewnianego, doskonale imitujące prawdziwe drewno).